Six Sigma methodologies provide businesses with a structured approach to minimize defects and boost efficiency. In this field, implementation can be challenging due to inconsistent practices and poor documentation. ProcessStreet, a workflow automation platform, addresses these issues by automating Six Sigma processes, enhancing collaboration, ensuring consistency, and integrating 6 Sigma principles into everyday workflows.
This article explores five essential Six Sigma tools and techniques and how ProcessStreet enhances their effectiveness for better quality management.
Key Takeaways
- ProcessStreet automates DMAIC workflows to streamline 6 Sigma implementation and ensure continuous improvement.
- Value Stream Mapping in ProcessStreet helps optimize workflows by eliminating inefficiencies and integrating real-time collaboration tools.
- ProcessStreet facilitates root cause analysis with Fishbone Diagrams, enabling teams to identify and address defects systematically.
- Pareto Chart integration in ProcessStreet allows businesses to prioritize high-impact issues for efficient problem-solving.
- Control Charts in ProcessStreet enable real-time monitoring, automated alerts, and recurring audits to maintain process stability.
1. DMAIC Methodology: Road to Continuous Improvement
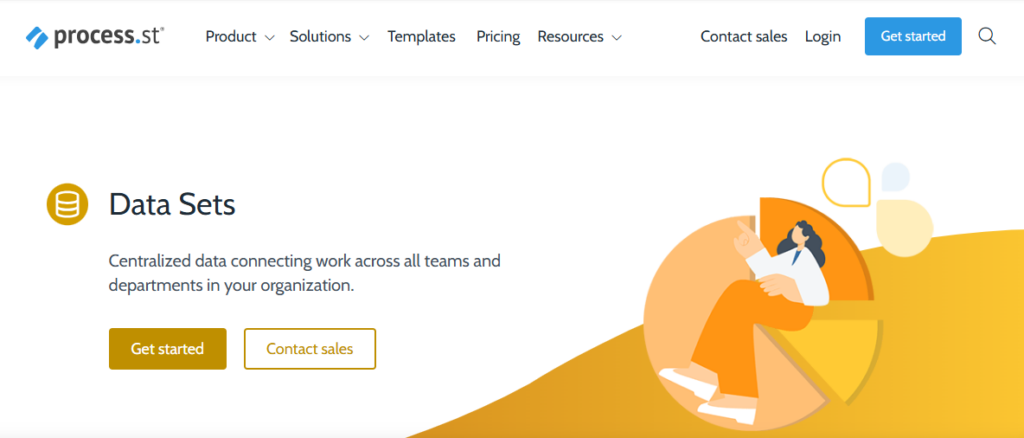
Source: process.st
DMAIC (Define, Measure, Analyze, Improve, and Control) gives teams a structured, data-driven method for continuous process improvements. Each step builds logically on the previous one, ensuring measurable and sustainable outcomes.
The DMAIC Process Simplified:
- Define – Clarify your objectives, problems, and voice of the customer’s expectations.
- Measure – Collect relevant data and set performance benchmarks.
- Analyze – Identify root causes of process issues using qualitative and quantitative techniques such as statistical tools.
- Improve – Implement targeted solutions to improve the process and boost efficiency.
- Control – Monitor processes to sustain the improvements you’ve achieved.
Example: Imagine experiencing delays in your shipping process. Using DMAIC with ProcessStreet, your team can quickly define the specific problem (late deliveries), measure shipping times and delays, analyze data to find bottlenecks, implement streamlined packing procedures, and then control the process through regular monitoring to maintain these improvements.
ProcessStreet’s DMAIC Benefits:
- Automated Checklists: Ensures consistency at each DMAIC stage, benefiting Master Black Belt professionals who oversee large-scale process improvements.
- Data Integration: Easily connects with analytics tools like Google Sheets, Tableau, and Power BI.
- Better Collaboration: Assign tasks and manage workflow oversight.
- Compliance Assurance: Built-in audit trails help maintain adherence to best practices.
2. Value Stream Mapping (VSM): Simplifying Workflow

Image Source: process.st
Value Stream Mapping visually illustrates your workflow, helping you pinpoint areas of inefficiency. It separates value-added from non-value-added tasks, enabling teams to eliminate waste and streamline operations strategically.
Example: Suppose your customer support workflow feels cluttered. ProcessStreet’s interactive Value Stream Mapping templates allow your team to visualize each step clearly, instantly identify unnecessary steps, like redundant approvals, and collaborate in real-time to simplify your workflow.
How Value Stream Mapping Works
Value Stream Mapping involves creating a detailed flowchart that outlines each step of a business process from start to finish. The goal is to:
- Visualize the current workflow – Identify the sequence of activities within a process.
- Analyze inefficiencies – Determine which steps add value and which ones cause delays or redundancy.
- Optimize and streamline – Implement changes that improve efficiency while maintaining quality.
By mapping out the entire workflow, teams can use 6 Sigma tools and methodologies to identify unnecessary approvals, redundant data entry, or delays in decision-making.
ProcessStreet’s VSM Features:
- Interactive Templates: Easy-to-use maps to visualize and refine processes.
- Real-Time Approvals: Instant reviews and validations to keep things moving.
- Dynamic Collaboration: Teams can update maps collaboratively, adapting quickly to change.
- Visual Tool Integration: Seamlessly integrate with popular diagramming tools like Lucidchart and Miro.
3. Fishbone Diagram: Getting to the Root of Problems
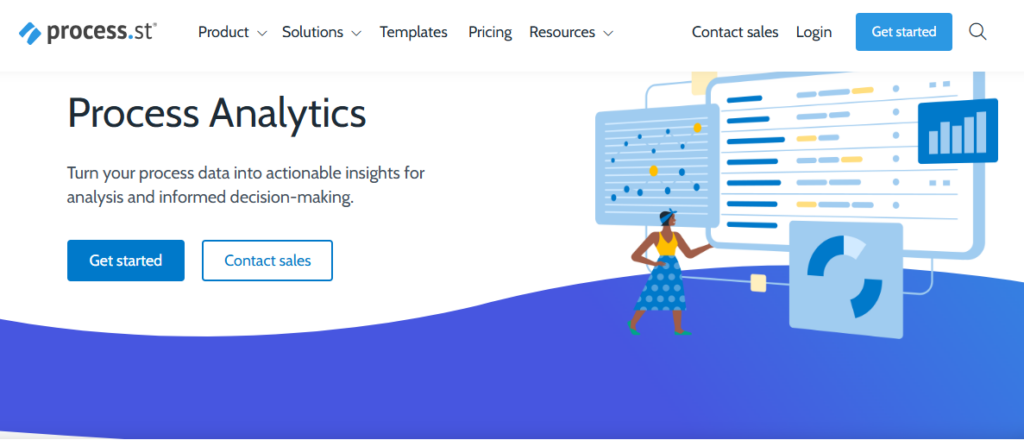
Image Source: process.st
Fishbone Diagrams help systematically identify and categorize potential root causes of quality issues, breaking down complex problems into understandable parts.
Example: If product defects are increasing, a Fishbone Diagram in ProcessStreet helps your team systematically explore potential reasons, such as outdated equipment (Machines) or inadequate training (People, quickly guiding your team toward practical solutions.
How the Fishbone Diagram Works
The Fishbone Diagram organizes causes into six key categories that can contribute to an issue:
- People – Human-related factors such as inadequate training, skill gaps, or lack of communication.
- Methods – Process inefficiencies, outdated procedures, or inconsistent workflows.
- Machines – Equipment failures, outdated technology, or inadequate maintenance.
- Materials – Defective or low-quality raw materials affecting production.
- Measurements – Errors in data collection, lack of proper metrics, or inaccurate analysis.
- Environment – External factors include workspace conditions, supply chain disruptions, or regulatory issues.
ProcessStreet’s Fishbone Advantage
ProcessStreet streamlines root cause analysis by providing structured, automated, and collaborative tools, making it a valuable resource for Lean 6 Sigma Black Belt professionals.
- Easy-to-use Templates: Standardize root cause documentation for clarity.
- Task Assignments: Engage your team members actively in solving problems.
- Conditional Logic: Guides your team towards practical, data-driven solutions.
4. Pareto Chart: Focusing on What Matters Most
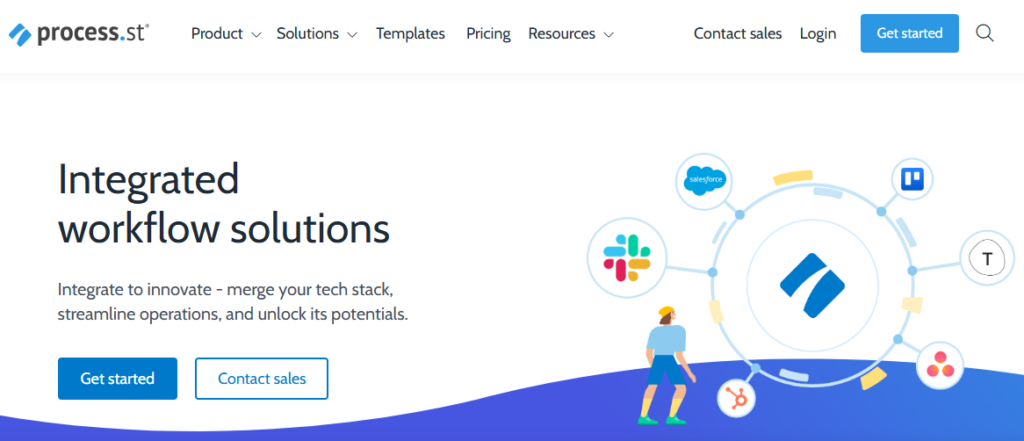
Image Source: process.st
The Pareto Chart applies the 80/20 principle to help your business prioritize issues that have the most significant impact on quality, effectively directing resources where they’ll have the most significant effect.
Example: If customer complaints are piling up, ProcessStreet’s Pareto Chart integration automatically tracks and visualizes recurring complaints, quickly revealing the 20% of issues causing 80% of the dissatisfaction, allowing you to prioritize effectively.
ProcessStreet Makes Pareto Analysis Simple:
- Automatic Data Collection: Easily document recurring issues.
- Integrated Visualization Tools: Use tools like Google Sheets or Power BI for instant visual insights.
- Prioritized Approvals: Address critical issues first, making the most of your team’s efforts.
- Regular Progress Checks: Consistent monitoring ensures continuous improvement.
5. Control Charts: Keeping Processes Stable
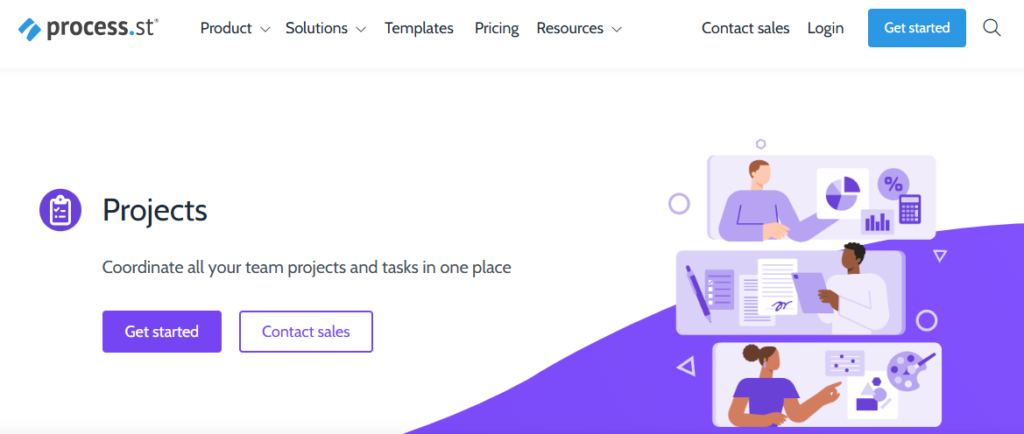
Image Source: process.st
Control Charts monitor processes over time, quickly identifying variations and assessing process capability so you can take preventive actions and maintain high quality consistently.
Example: If your production occasionally faces quality inconsistencies, ProcessStreet’s Control Charts automatically alert your team when production deviates from set standards, enabling proactive resolution before issues escalate.
Control Chart Support from ProcessStreet:
- Real-Time Data Collection: Quickly detect deviations from expected performance.
- Automated Alerts: Get immediate notifications for potential issues.
- Historical Documentation: Keep track of process changes for ongoing improvements.
- Scheduled Audits: Regular reviews help sustain your quality standards.
Six Sigma vs. Lean Six Sigma: Best with ProcessStreet?
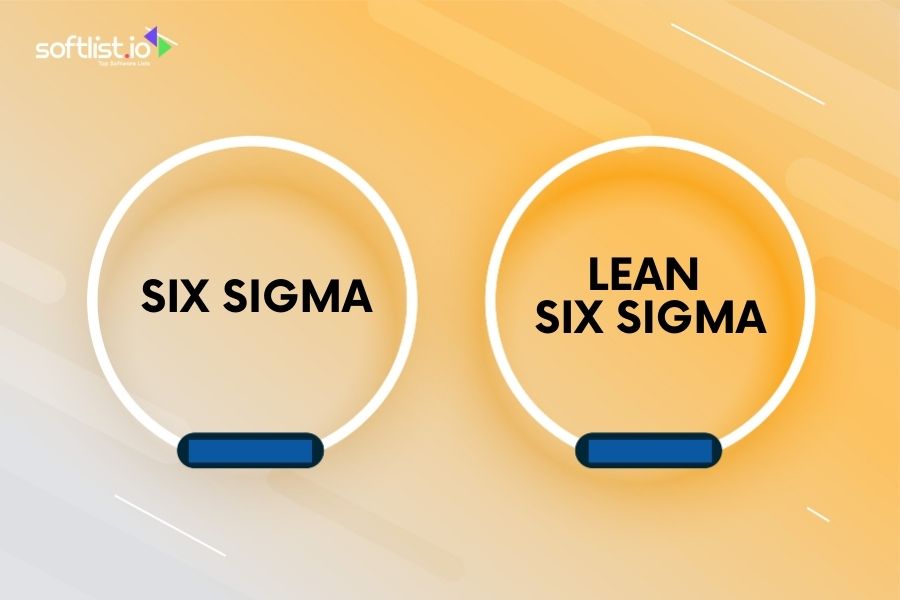
Six Sigma and Lean Six Sigma are powerful methodologies and tools for optimizing manufacturing processes, improving efficiency, and reducing defects. However, they differ in their approach to process improvement and execution.
How ProcessStreet Supports Both Methodologies
ProcessStreet enhances both Sigma implementation through automation and workflow management, ensuring businesses can efficiently track, document, and optimize each phase of the DMAIC methodology.
- For Six Sigma:
- Automates data collection for the phase of DMAIC, improving decision-making.
- Provides Six Sigma resources for training and certification tracking.
- Supports compliance through built-in audit trails.
- For Lean Six Sigma:
- Enables powerful tools like Value Stream Mapping and process automation.
- Reduces errors in real-time through checklists and production process monitoring.
- Enhances collaboration between One Sigma and senior-level teams.
Which One Works Best with ProcessStreet?
Both methodologies work seamlessly with ProcessStreet, but Lean 6 Sigma benefits more from workflow automation and process optimization tools. Companies seeking Black Belt training or to master Six Sigma can integrate ProcessStreet for a structured, data-driven approach to business efficiency.
Why Choose ProcessStreet for Your Six Sigma Implementation?
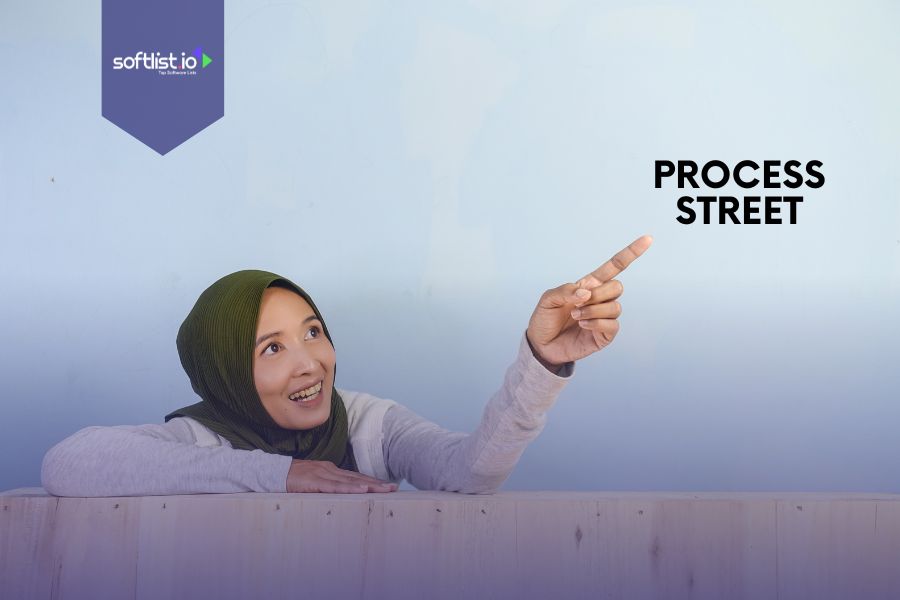
Implementing Six Sigma successfully requires a structured approach, consistent execution, and seamless collaboration. ProcessStreet enhances the effectiveness of Six Sigma methodologies by providing a powerful workflow automation platform to support improvement projects.
This supports professionals seeking Six Sigma Certification, benefiting practitioners from Green Belt to Master Black Belt levels. That simplifies process improvement, ensures compliance, and fosters continuous innovation.
Key Benefits of ProcessStreet in Six Sigma Implementation
1. User-Friendly Interface for Rapid Adoption
- Challenge: Six Sigma methodologies can be complex and require significant training.
- How ProcessStreet Helps: Its intuitive interface allows teams to easily adopt and implement Six Sigma processes with minimal training, even for those new to the methodology. The interface also caters to Six Sigma experts.
2. Automated Documentation for Compliance and Traceability
- Challenge: Manual documentation leads to errors, inefficiencies, and compliance risks.
- How ProcessStreet Helps: Automates process documentation, ensuring that every step in the Six Sigma framework (DMAIC, VSM, Fishbone Diagrams, etc.) is recorded accurately for compliance, audits, and process tracking.
3. Real-Time Collaboration for Efficient Problem-Solving
- Challenge: Disconnected teams and delayed communication slow down Six Sigma projects.
- How ProcessStreet Helps: It enables seamless team collaboration with real-time approvals, notifications, and task assignments, supporting Sigma and Lean Six Sigma initiatives and ensuring faster problem identification and resolution.
4. Scalability to Support Large-scale Six Sigma Projects
- Challenge: Six Sigma needs to be applied across departments and scaled effectively.
- How ProcessStreet Helps: Adaptable for small teams and enterprise-wide Six Sigma initiatives, from Six Sigma Black Belt leaders to frontline employees, ensuring a standardized approach across the organization.
5. Customizable Templates for Standardized Six Sigma Workflows
- Challenge: Creating Six Sigma frameworks from scratch is time-consuming.
- How ProcessStreet Helps: Provides ready-made, customizable templates for DMAIC, Value Stream Mapping, Root Cause Analysis, and more to support Six Sigma initiatives, allowing organizations to implement Six Sigma without reinventing the wheel.
6. Integration Capabilities for Data-Driven Decision-Making
- Challenge: Six Sigma relies heavily on data analysis from multiple sources.
- How ProcessStreet Helps: Integrates seamlessly with analytics tools like Google Sheets, Power BI, and Tableau to provide real-time insights for informed decision-making.
7. Continuous Improvement Culture through Recurring Workflows
- Challenge: Sustaining Six Sigma improvements over time is difficult.
- How ProcessStreet Helps: Automates recurring checklists, scheduled audits, and process monitoring, ensuring ongoing quality control and continuous improvement in every process through Six Sigma and Lean Six methodologies.
Conclusion
Integrating Lean and Six Sigma methods with ProcessStreet provides businesses with a practical, scalable solution to managing quality effectively. By combining workflow automation, real-time process monitoring, and enhanced team collaboration, companies can quickly achieve and maintain continuous improvement using frameworks like 5S.
Ready to elevate your Six Sigma initiatives? Softlist.io can guide you to the right workflow automation solutions, including ProcessStreet, helping your business reduce waste, enhance quality, and stay ahead of the competition.
FAQs
What Is Six Sigma, and Why Is It Important?
Six Sigma is a data-driven methodology that helps businesses reduce defects, improve efficiency, and enhance customer satisfaction. It identifies and eliminates process variations to create consistent and high-quality products or services.
Using Six Sigma, organizations can streamline operations, minimize waste, and achieve continuous improvement.
Is ProcessStreet Suitable for Businesses New to Six Sigma?
ProcessStreet is ideal for businesses new to Six Sigma because it provides easy-to-use templates, step-by-step workflows, and automation tools that simplify process improvement.
Even teams without prior Six Sigma experience, such as those pursuing a Six Sigma Green Belt, can follow structured processes, including those at the Lean Six Sigma Green Belt level, ensuring consistency and efficiency. Its intuitive interface allows businesses to gradually integrate Six Sigma methodologies at their own pace.
How Does ProcessStreet Handle Data Security and Compliance for Six Sigma Processes?
ProcessStreet prioritizes data security by offering encrypted storage, role-based access control, and audit logs to track workflow changes.
To protect sensitive business data, it complies with industry standards such as GDPR and SOC 2. Organizations can maintain compliance by documenting process changes, approvals, and corrective actions in a secure environment.
Can ProcessStreet Integrate with Other Software Tools Used in Six Sigma Projects?
ProcessStreet integrates with various software tools like Google Sheets, Power BI, Lucidchart, Zapier, and Slack, enhancing workflow automation and data tracking.
These integrations help businesses visualize process improvements, collaborate in real-time, and make data-driven decisions, as they are commonly used to improve processes. By connecting with existing software, ProcessStreet enhances the effectiveness of Six Sigma initiatives.
How Can ProcessStreet Help Businesses Sustain Six Sigma Improvements over Time?
ProcessStreet supports long-term Six Sigma success by automating recurring checklists, scheduling audits, and sending notifications for process deviations.
Continuous monitoring through real-time data tracking ensures that businesses can quickly detect inefficiencies and improve existing processes. This approach helps organizations maintain process improvements, prevent regression, and drive continuous quality enhancements.